Guide to Inventory Audits: Best Practices & Tips
The infamous inventory audit - arguably the most tedious process for eCommerce, retail and any other business that stores goods within a warehouse. Is your inventory all there? Does it match your financial records? Is everything labelled properly?
Yes, these may be the questions that haunt business owners, but answering them can ensure that everything is as it should be. And, if it’s not, then you can quickly identify the issue and resolve it before things might get out of hand.
This is precisely why inventory audit procedures are of vital essence and must be conducted frequently, in order to avoid potential issues down the line. Now, you’re probably feeling exhausted just by thinking about doing a manual inventory check, aren’t you?
There’s no reason to feel that way. Although the process may seem overwhelming at first, there are audit procedures for inventory analysis that will make everything more seamless and thus, ensure you won’t get any headaches along the way. Well, let’s dig into it then, shall we?
What Exactly is an Inventory Audit?
Even though an inventory audit can be a complex process, it can, however, be described in simple terms.
That said, an inventory audit refers to the process of cross-checking inventory records against your company’s financial records, in order to ensure that everything matches.
The purpose of this procedure is to ensure inventory accuracy and spot any potential issues that may or may not have occurred.
Why Do Inventory Audits Matter?
You do want to make sure that all the goods or raw materials you’ve procured are accounted for, no? After all, it’s not like your business depends on accurate inventory or anything.
Jokes aside, it may seem like you’re just counting chickens with inventory audits, but there’s much more to the whole process than it meets the eye. So, here’s why auditing your inventory regularly matters that much.
- Inventory discrepancies - An audit allows you to notice any differences between inventory and financial records. If that’s the case, then you can easily spot where the issue may have occurred, so that you can investigate further.
- Stock limits - As you may already know, asset management is of the utmost importance for eCommerce businesses. That said, identifying overstocking or understocking issues is simply crucial for ensuring you don’t overspend on products you don’t need as much, or that you run out of products in high demand.
- Potential theft - If the records don’t match, that is quite a cause for concern. Perhaps, there’s an error in the records themselves or maybe, someone is helping themselves to your stuff. Either way, you have to get to the bottom of the issue and only an inventory audit can help you notice such things, to begin with.
- You’re bound to have it as a public record - In most cases, your inventory audit is required by law, especially if your inventory stock is labelled as an asset on your balance sheet.
For instance, the UK’s FRC (Financial Reporting Council) is responsible for promoting transparency and integrity in business. They set the UK Corporate Governance standards that are indicated in the ISA [1] UK and [2] Ireland 501 Audit Evidence—Specific Considerations for Selected Items.
Best Practices for Optimising Your Inventory Audits
Now that we’ve gone over why you need inventory audits, it’s time to take a peek at how to make the tedious process more seamless and perhaps even enjoyable.
In all honesty, no one enjoys an audit, but by implementing the right strategies and by leveraging the right technological tools, you can make an audit feel less like a chore and more like just another, yet still important, process in your supply chain.
1. Physical Inventory Count
Yes, this strategy is as mundane as it sounds like, but that doesn’t make it any less efficient than it actually is. One would think that with all the modern technology, you’ll no longer have to physically count every single item in your warehouse. You do, or at least, you should.
With physical counting, you’re going step-by-step through all of your inventory, while crossing things off the financial record as you proceed. This is actually the best way to ensure that everything is accounted for. Not only that but if your items are properly labelled using barcodes or RFID, a corresponding scanner should make a physical count a breeze.
2. Cutoff Analysis
With this strategy, you’re basically halting all procurement and shipment operations, in order to conduct a physical inventory count, hence the name “cutoff”. But why would you do such a thing?
Well, for starters, by cutting off all your operations, you ensure that no goods from your stock get processed while you count inventory. As you may imagine, having new items coming in or having products shipped whale you perform an audit can easily lead to a disaster.
Suddenly, you have more goods than you thought you do or there are goods missing that should be in the warehouse. Before you know it, you’re investigating everything and everyone just because you didn’t halt operations and items were processed by your staff as intended, blissfully unaware that you had an audit in mind.
3. Cycle Counting Your Inventory
Similar to physical count, cycle counting your inventory focuses on monitoring your most valuable items in stock. These are often the fastest-selling products that are highly sought-after by your customers.
So what you do is perform more frequent audits on selected items only and physically count them to ensure you never run out of stock, as well as ensure that those inventory levels are constantly at optimal levels.
4. Finished Goods or Overhead Analysis
Now, this strategy isn’t necessary, per se. It’s purely optional, but if you do want to run a smooth business operation, you should give it some thought. That said, finished goods analysis, otherwise known as overhead analysis, takes non-inventory aspects into consideration. Thisoften includes rent, utility, bills, staff salaries and so on.
Now, this may not have much to do with your inventory but it’s correlated nonetheless. After all, everything happens in your warehouse, so taking overhead expenses into consideration gives you a clearer picture regarding just how much your business operations actually cost. Now why does this even matter?
Simply put, it helps put budgeting into perspective. If you understand the overall costs, you can plan for restocking and resupplying of inventory accordingly, as well as aid you with demand planning. It also helps you minimise waste and maximise efficiency, which is quite essential if you wish to be a successful store owner.
5. The Cost of Freight Services
Operating internationally isn’t uncommon for eCommerce businesses. Many online stores ship goods overseas and import the same from different countries.
An expensive endeavour to be sure, but also a lucrative one, provided you’re organised well and have a global network of fulfilment services at your disposal.
If that’s the case, conducting the cost of freight services analysis is essential for your international success. Freight forwarding, customs brokerage and international import/export of goods costs money.
Knowing just how much everything costs allows you to plan how and when the goods will arrive at their destination, as well keep track of any and all items that may have been lost or damaged during transport.
6. ABC or High-Value Inventory Analysis
Every eCommerce store has an assortment of goods that are the best-selling products. These products are often the ones that bring in the most revenue compared to the rest of the inventory.
Categorising products based on their value within a fulfilment centre, therefore, allows you to prioritise goods that are moving in and out faster than the rest. As you may already know, this ensures there are no delays for procurement or shipment of these fast-moving items.
That’s why high-value products are classified as category A, while mid-tier and low-value products are classified as category B and C respectively. For example:
- Category A consists of 20% of your inventory
- Category B consists of 30% of your inventory
- Category C consists of 50% of your inventory
At the same time:
- Category A yields 70% of your revenue
- Category B yields 20% of your revenue
- Category C yields 10% of your revenue
Aside from prioritising, ABC analysis allows you to plan how to store each category of products within your warehouse. So, for instance, category A products should be kept somewhere safe and secure, in order to avoid damages, costly mistakes or even potential theft.
Conversely, Category C items should be kept somewhere close to the exit of the warehouse. You want to move these items through sales, discounts and coupons so they don’t block everything else and take too much space all the time.
Tips for Improving Your Inventory Audit Process
Now that we’ve gone over some of the best practices regarding how to perform an inventory audit, it’s time to see how to boost the efficacy of the entire process. After all, why complicate things when you can leverage tools and technology to ease the workflow?
Question is, which approach to take. Well, that depends entirely on your business needs and means. However, the best approach is to combine multiple approaches into a unified orchestrated solution. That said, here are a few tips that should help you make the right decision.
- Leverage the right technology - Consider implementing inventory management software, warehouse management software and automation tools, to name a few.
- Outsourcing - If you lack anything in-house, consider outsourcing some of the audit tasks to a 3PL (Third Party Logistics) company. The only thing you have to do is find a company that can tailor their procedures to your company’s needs.
- Schedule an audit in advance - Inventory audit is not a surprise inspection. There’s absolutely no need to introduce more chaos into the process, which is why you should schedule it in advance. Your best bet is when the business is slow and when halting operation won’t impact order fulfilment as it would during peak performance.
- Investigate right away - If your inventory audit shows any potential issues or mismatch in the records, don’t sit and wait for a problem to go away on its own. It wont. Instead, act immediately and investigate the source so you can understand when, why and where the problem occurred. This helps prevent future issues from arising again.
Checklist for Your Inventory Audit
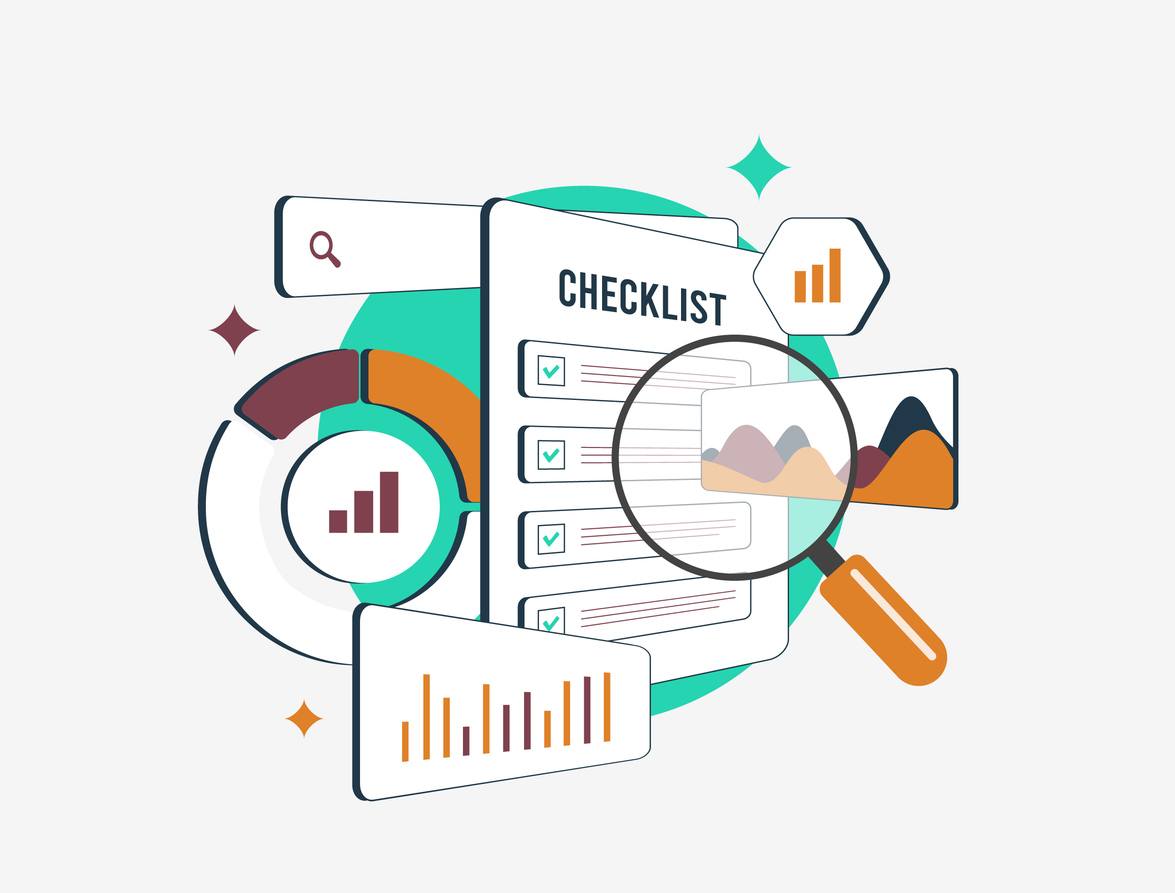
The very process of performing an audit can be quite confusing, at least until you get used to it. This is why you should adequately prepare, so that you don’t miss out on anything important. For that purpose, here’s a checklist that should help you get everything you need and help you set up an audit properly.
- As mentioned before, pick the right moment to conduct an audit, preferably when your company isn’t operating at full potential.
- If you’re outsourcing audit tasks to a third-party company or some other external auditor, make sure you provide them with all the information they need to do their job accordingly.
- Decide which are the best strategies for the audit. This may include physical count, overhead analysis, ABC analysis and so on.
- Thoroughly record any and all findings during the audit. It’s recommended to have both written and computerised copies of your records just in case. You can pick one or the other, or both if it suits you.
- Investigate any discrepancies or item reconciliations you come across during an audit immediately.
Make Inventory Audits Less Painful With Bezos
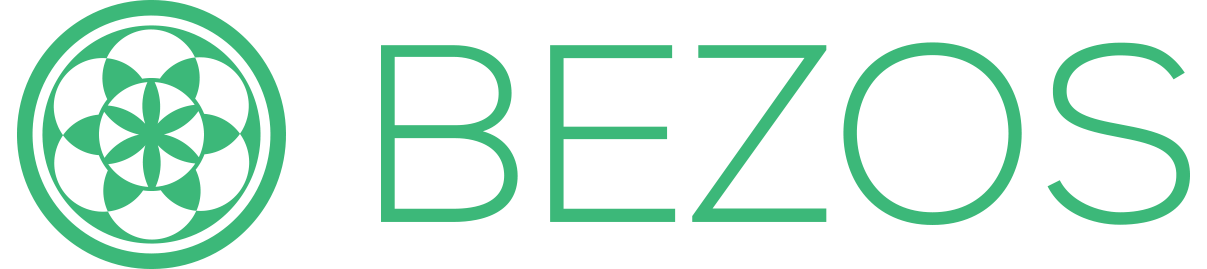
It’s a well-known fact that audit inventory procedures can oftentimes be quite overwhelming and a bit too demanding for eCommerce businesses. This is especially true if your online store is new in the market and you don’t know what to do or how to do it.
After all, you need the right resources and system in place to ensure everything is in order. But, if you cannot manage that on your own, Bezos is here to help you out. Our business specialises in every aspect of eCommerce fulfilment logistics, including inventory audits.
So if this process is giving you reason for pause, don’t hesitate to choose us as your outsourcing partner and we will make short work of any and all audit issues you may have. Reach out to us today, and we’ll come up with a quote tailored to your business needs.
Conclusion: Don’t Fear the Audits
An inventory audit should not be seen as something awful like a surprise inspection from the HM Revenue & Customs (HMRC) or the IRS. This type of an audit is good for your business and conducting it may be tedious. but nonetheless necessary.
After all, if you don’t keep track of your inventory, you will most likely make a costly mistake with potentially disastrous consequences. That said, there is always a way to make complex procedures seamless and streamlined, so you don’t have to lose any sleep over it.
All that is needed is for you to plan accordingly and leverage the right approach that will make inventory audits, efficient, accurate and most importantly, painless for everyone involved.
FAQ:
Is inventory auditing hard?
Technically, it is, but it doesn’t have to be. As mentioned before, with the right strategies and tools even something as complex and mundane as an inventory audit can be made seamless and simple. In the end, everything comes down to choosing the right approach.
What is the difference between inventory audit and stock audit?
None. Stock audits are commonly referred to as inventory audits. Which term you’ll use depends on the region your online store operates in. Stock and inventory are one and the same so it’s really up to you which terminology you’ll opt for.
What is the risk of inventory audit?
Every inventory audit carries a certain risk for both the company and the end-consumers or customers, if you will. First of all, if you want an accurate audit, you have to halt operations. And since audits are time-consuming, this may affect your business and order fulfilment to some degree.
Moreover, if you don’t keep a clean record of everything you’ve analysed during the audit, you might miss out on potential issues that can grow into serious problems if left unchecked and unresolved.
What are the assertions for audit of inventory?
The end of every inventory audit is tested by comparing the results with certain assertions. In most cases, auditors will conduct this test so you don’t have to. Assertions may vary based on inventory and the nature of your business, (i.e operating internationally or not) but the most common ones include:
- Existence
- Completeness
- Rights and Obligations
- Valuation
- Presentation and Disclosure