OTIF Meaning: What Is OTIF in Logistics?
Picture this: every order you ship reaches its destination precisely when expected, with the exact quantity needed — no delays, no shortages. This is the essence of On-Time In-Full (OTIF), a critical metric that defines success in the world of logistics. But what is the full OTIF meaning, and why does it hold such importance for your supply chain operations?
In this article, we’ll explore what OTIF is, why it’s essential for your OTIF supply chain, and how it’s calculated. We’ll also address common challenges and offer strategies to help you improve your OTIF scores. Finally, we’ll introduce you to Bezos, a Fulfilment-as-a-Service (FaaS) platform that helps eCommerce brands optimise their OTIF supply chain performance, ensuring your products are delivered on time and in full, every time.
What Is OTIF?
OTIF (On-Time In-Full) is a critical performance metric in supply chain management that measures a company’s ability to deliver orders as promised — both in terms of timing and quantity. It reflects how effectively a company manages its logistics, impacting customer satisfaction and overall operational efficiency. We explore this in more detail below!
Introduced by Walmart in 2017 to track supplier performance[1], OTIF quickly became a popular metric for evaluating supply chain reliability. By focusing on the accuracy and timeliness of deliveries, this metric helps businesses identify and address weaknesses in their supply chain processes.
Why Is OTIF Important?
There are numerous reasons why OTIF is an essential metric to monitor and optimise, including:
- Customer Satisfaction: Consistently meeting delivery promises enhances customer loyalty and reduces the likelihood of complaints and returns. In industries like eCommerce, where customer retention is vital, maintaining a strong OTIF score is a must.
- Operational Efficiency: It helps companies identify inefficiencies in their supply chain which, in turn, can help them to streamline operations, reduce waste, and optimise inventory management.
- Business Relationships: High OTIF scores strengthen relationships with companies and partners, potentially leading to better contracts and long-term collaborations.
- Financial Impact: Poor OTIF performance can result in penalties, lost sales, and increased costs. On the other hand, excelling in OTIF can lead to cost savings and increased revenue, as efficient supply chains are less likely to incur the costs associated with delays and shortages.
How to Calculate OTIF
Now we know the OTIF meaning, let’s discuss how to calculate it.
The basic formula for OTIF is:
OTIF = (Number of Orders Delivered On-Time and In-Full / Total Number of Orders Delivered) × 100
Example of an OTIF Calculation
Let’s consider a simple example to illustrate this:
- Suppose your company delivered 1,000 orders last month.
- Out of these, 850 orders were delivered on time and with the correct quantities.
Using the OTIF formula:
OTIF = (850 / 1000) × 100 = 85%
This means that 85% of your orders were delivered as promised, reflecting your OTIF performance.
Ensuring Accuracy in OTIF Calculations
Accuracy in OTIF calculations is vital for maintaining reliable performance data. Miscalculations can distort your understanding of supply chain efficiency and lead to misguided decisions. Therefore, it’s essential to use accurate data, regularly review calculations, and address any inconsistencies promptly to ensure that your OTIF metrics truly reflect your operational performance.
For more insights on how to manage your logistics efficiently, check out our guide on shipping logistics.
What Is a Good OTIF Benchmark?
Determining a good OTIF benchmark is essential. It is important to note that these benchmarks can vary significantly across industries. Generally speaking, 80% - 90% is considered a good score. However, industries where delivery timing is less critical, for instance, may find that a lower OTIF score is acceptable.
Setting the Right OTIF Target
To set an appropriate OTIF target, consider the following:
- Understand Industry Standards: Research typical OTIF benchmarks within your industry to establish a baseline. This helps ensure your targets are competitive and aligned with industry expectations.
- Evaluate Customer Needs: Tailor your OTIF targets to meet customer expectations. In industries where customers expect fast and accurate deliveries, setting a higher OTIF target is crucial to maintaining customer satisfaction and loyalty.
- Monitor and Adapt: Regularly review your OTIF performance and be ready to adjust your benchmarks as your business evolves.
Setting the right OTIF benchmark is about finding a balance that challenges your business to improve while being realistic about the complexities of your supply chain.
For more guidance on optimising your operations, explore our comprehensive logistics plan.
Understanding and Overcoming Common OTIF Challenges
There are several common obstacles which can make maintaining a high OTIF score challenging. Below, we list several of them, along with some helpful improvement tips to help overcome them:
- Supply Chain Complexity: Global supply chains with multiple suppliers and logistics providers increase the risk of delays and errors, making it harder to achieve high OTIF scores.some text
- Improvement Tip: Streamline your supply chain by consolidating suppliers where possible and implementing advanced supply chain management software. This can help reduce the number of touchpoints and improve overall coordination, leading to fewer errors and delays.
- Demand Forecasting Errors: Inaccurate demand forecasting can lead to issues like stockouts or overstock, which can negatively impact OTIF.some text
- Improvement Tip: Enhance demand forecasting accuracy by leveraging machine learning algorithms and real-time data analytics. These tools can help predict demand more accurately, reducing the risk of stockouts and ensuring that inventory levels are aligned with customer needs.
- Transportation Delays: Delays caused by weather, traffic, or logistical issues can result in late deliveries, while poor coordination can lead to incomplete shipments.some text
- Improvement Tip: Implement real-time tracking and dynamic routing software to optimise transportation routes and minimise delays. Additionally, maintain strong relationships with reliable logistics providers who have a proven track record of meeting delivery deadlines.
- Supplier Reliability: Unreliable suppliers can disrupt the entire supply chain, affecting OTIF due to production delays or quality control issues.some text
- Improvement Tip: Establish strong partnerships with your suppliers through regular performance reviews and clear communication of your OTIF expectations. It may be worth considering diversifying your supplier base to reduce dependency on any single supplier and mitigate risks.
- Inventory Management: Issues like inaccurate inventory counts, inefficient warehousing, or slow order processing can prevent timely and complete deliveries.some text
- Improvement Tip: Optimise inventory management by implementing real-time inventory tracking systems and adopting just-in-time (JIT) practices where feasible. This will help ensure that inventory levels are accurate and aligned with demand, reducing the risk of delays in fulfilling orders.
Did You Know? JIT practices involve managing inventory so that materials and products are delivered exactly when they are needed in the production process, minimising storage costs and reducing waste.
Bonus Tips for Optimising Your OTIF Score
- Prioritise High-Value Orders: Implement a prioritisation system where high-value or time-sensitive orders are processed and shipped first, like next-day deliveries. This ensures that critical orders meet OTIF targets even during peak periods or disruptions.
- Regularly Update Safety Stock Levels: Adjust your safety stock levels based on seasonal demand fluctuations or changes in supplier reliability. This helps buffer against unexpected demand spikes or supply chain delays, maintaining OTIF.
- Utilise Gamification for Employee Engagement: Introduce gamification elements in your warehouse or logistics operations to motivate employees. Offering incentives for meeting or exceeding OTIF goals can improve overall performance.
The Role of Technology and Visibility Tools in Optimising OTIF
As we can see from our improvement tips, technology and visibility tools can be a valuable asset when it comes to enhancing OTIF performance and ensuring businesses meet their OTIF supply chain goals. By using tools like real-time tracking systems, cloud-based platforms, and Internet of Things (IoT) sensors, companies gain full visibility over their operations. This allows them to quickly respond to disruptions, reduce errors, and ensure that orders are delivered on time and in full.
How OTIF Compares to Other Supply Chain KPIs
Now that we have a strong understanding of OTIF, let’s briefly consider how it relates to other common supply chain key performance indicators (KPIs):
Why Choose Bezos for Your Fulfilment Needs
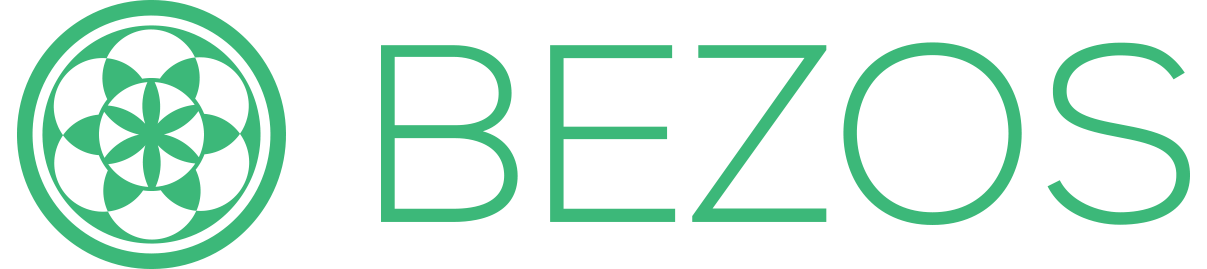
Maintaining a high OTIF performance is crucial for eCommerce brands. At Bezos, we focus on optimising OTIF by providing streamlined and efficient fulfilment services that ensure your products reach customers on time and in full.
Why should you choose us? Bezos offers tailored solutions to help small and medium-sized eCommerce businesses access fulfilment and logistics services typically reserved for larger companies. Here are just a few of our benefits:
- Comprehensive Fulfilment Services: We take care of your entire fulfilment process, including storing your inventory, pick and pack services, returns management, and value-added services such as kitting and bundling.
- Multi-Channel Integration: Our platform seamlessly integrates with over 30 channels, including Shopify, Amazon, and WooCommerce.
- Real-Time Order Visibility: Our fulfilment services provide you with real-time insights into all your orders via an intuitive, easy-to-use portal. This ensures full transparency and control over your supply chain, helping you meet your OTIF goals with confidence.
- Flexible Shipping Services: With access to over 100 shipping providers, we offer flexible delivery choices, helping you maintain a strong OTIF score even during busy periods.
- Dedicated Support: Our account managers work closely with you to ensure that every aspect of your fulfilment runs smoothly, offering continuous 24/7 support.
- Global Fulfilment Network: With fulfilment centres across the UK and EU, we enable businesses to expand into new markets.
To learn about how we have already helped businesses, check out our success story with Enjoy The Drop. With the help of our services, they grew 12x in the UK and were primed to launch in new geographies!
Partnering with Bezos gives you access to a seamless and efficient fulfilment system that enhances your OTIF performance, allowing you to focus on growing your brand. For expert fulfilment services, look no further than Bezos!
Closing Thoughts on OTIF
Understanding the OTIF meaning and its importance in supply chain management is crucial for businesses looking to enhance operational efficiency and customer satisfaction. By focusing on optimising this metric, you can ensure that your deliveries meet expectations in both timing and quantity. Ultimately, a strong OTIF score leads to better business relationships and financial gains. For businesses aiming to improve their OTIF supply chain, partnering with expert fulfilment services like Bezos can make all the difference.
FAQs
How is OTIF calculated?
OTIF is calculated using the formula: (Number of Orders Delivered On-Time and In-Full / Total Number of Orders Delivered) × 100.
What is an example of OTIF?
If a company delivers 850 out of 1,000 orders on time and in full, the OTIF score is 85%.
What is OTIF slang for?
OTIF stands for “On-Time In-Full,” a supply chain management metric used to measure delivery performance.
What is the difference between OTD and OTIF?
OTD (On-Time Delivery) measures whether orders are delivered by the promised date, while OTIF considers both on-time and complete deliveries.
Referenzen
[1] https://uk.news.yahoo.com/walmart-start-fining-suppliers-early-153400509.html