Articles
What Are the Components of Fulfilment Costs?
Introduction
In the order fulfilment world, keeping track of costs is fundamental. These costs are not merely about transporting a product from point A to point B. They represent a detailed spectrum of operations, each contributing to the process that ends with a product in a customer's hands.
At Bezos, we know everything there is to be known about the components of fulfilment costs. That’s why we provide our customers with an expert order fulfilment solution that keeps costs down without compromising quality.
To prove our expertise, we will delve into the specific components that make up fulfilment costs and explore their impact on overall business operations. From warehouse and inventory costs to labour, shipping, and technology expenses, we will unfold the essential elements that together shape the concept of fulfilment costs.
Let's embark on this journey to gain a more profound understanding of these crucial aspects of business operations.
Points clés
- Understanding fulfilment costs is crucial for business expansion, as saving on these expenses allows for reinvestment in other areas.
- Fulfilment costs comprise various components, each of which impacts the bottom line and requires careful management. We can divide these components into warehouse, inventory, and shipping costs.
- Warehouse costs form the foundation of the fulfilment cost structure, while inventory costs involve expenses related to procuring, storing, and handling obsolete or excess stock. Lastly, shipping costs include packaging, labour, carrier charges, customs and duties, and return handling costs.
- By partnering with an expert fulfilment company like Bezos, businesses can transform their processes, unlock substantial savings, and explore new market opportunities on a global scale.
Fulfilment Costs: A Detailed Exploration
Learning how to keep fulfilment costs down is crucial for any business looking to expand. After all, every pound saved in fulfilment costs can be reinvested in other areas of your business. But you can’t learn how to save on fulfilment costs without a fair amount of knowledge about them.
If you ask us, understanding fulfilment costs is like holding a compass – it guides your business decisions, informs your strategy, and ultimately impacts your bottom line. By the time you finish reading this article, you will not only understand the various components of fulfilment costs but also be well-equipped to manage them more effectively.
Warehouse Costs: Building the Foundation
The cornerstone of the fulfilment cost structure is undeniably warehouse costs. Importantly, understanding warehouse costs starts with recognising that they aren't simply about the physical space. Indeed, rent or mortgage constitutes a large chunk, but the picture isn't complete without including utilities like electricity and water. After all, heating and cooling the warehouse are essential for maintaining the quality of goods, especially for sensitive items.
These are some of the most common warehousing costs:
Inventory Costs: The Nerve Centre of Your Assets
The very heart of your business lies within the products that fill up your inventory. In the context of fulfilment costs, inventory expenditures take into account the costs associated with procuring these products, storing them, and dealing with obsolete or excess stock.
By maintaining an optimal level of inventory, you can ensure that your assets don't become liabilities. Careful management of inventory costs is not only about controlling the outflow of cash but also about preserving the value of your assets. This includes monitoring and minimising the cost of goods sold (COGS), optimising inventory holding costs, and reducing the costs associated with obsolete or excess inventory.
Plus, it’s also about managing your stock. We’re talking about things like placing orders when you’re low on stock or ensuring that you’re not over-ordering.
Picking and Packing – The Core of Inventory Costs
Picking and packing costs form the next significant component of inventory costs. Picking refers to the process of selecting the right products from your warehouse storage to fulfil an order. Packing, on the other hand, involves preparing these picked items for dispatch.
Each of these operations requires time, labour, and resources, and their cost-effectiveness is heavily dependent on the efficiency of your picking and packing processes. While picking and packing may seem straightforward, they involve a significant degree of complexity.
The cost of picking, for instance, can be influenced by the layout of your warehouse, the type of storage systems used, and the accuracy of your inventory records. On the other hand, packing costs depend on the materials used, the complexity of packing requirements, and the efficiency of your packing operations.
To manage these complexities, many companies choose to partner with an expert fulfilment company like Bezos that possesses the necessary know-how and resources. Simply, with our vast expertise and advanced systems, we can introduce economies of scale and enhance operational efficiency in handling your inventory.
Shipping Costs: The Journey of Products From Warehouse to Customer
No discussion on fulfilment costs can be considered complete without addressing the last step of the fulfilment process: shipping. From the warehouse to the customer's doorstep, each parcel's voyage involves a host of processes and expenses, all of which collectively form the shipping costs.
When we think about shipping, the first thing that comes to mind is often the logistics involved in getting the product from A (the warehouse) to B (the customer). However, a less obvious but essential aspect of shipping costs is the handling of returns or 'reverse logistics’. The process of receiving, inspecting, restocking, or disposing of returned items also involves labour, resources, and space, all of which come at a cost.
Some of the most common shipping expenditures are:
All these factors underline the complexity of managing shipping costs. However, with effective strategies, such as negotiating better rates with carriers, optimising packaging, and improving return management, these costs can be significantly reduced.
Spend Less on Fulfilment With Bezos
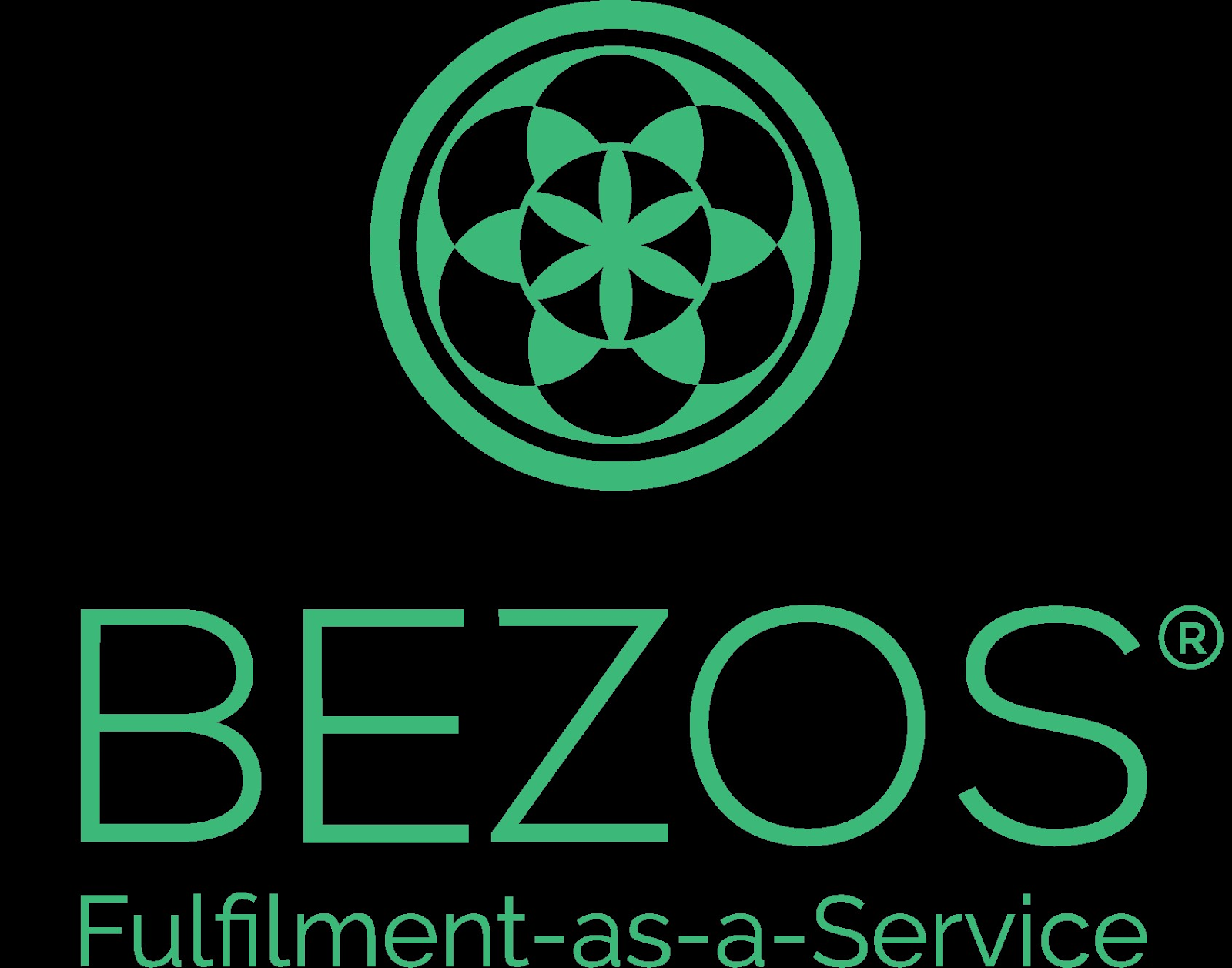
Are you exploring avenues to optimise your fulfilment process and drive savings in your business? Consider Bezos – your proficient partner in the world of goods fulfilment services, committed to augmenting efficiency in your import operations.
Leveraging an extensive network of distribution centres within the UK and fulfilment hubs in 16 additional countries, Bezos is equipped to elevate your eCommerce business on a global scale while maximising cost-efficiency.
What sets Bezos apart from the crowd of fulfilment service providers? We pride ourselves on our comprehensive and automated service offering, aimed at enhancing your import process in a way that is economical and efficient. We respect the fact that every business is different, so we're flexible enough to integrate your specific needs into our operations.
We also recognise that order fulfilment can sometimes be fraught with unforeseen challenges. That's why Bezos places immense value on transparency and responsiveness. Our customers have access to detailed shipment tracking, and we ensure all inquiries receive a response within a two-hour window. But perhaps the most appealing benefit we offer is flexibility in terms of contractual obligations. We don't tie our customers down with lengthy, binding contracts.
So if Bezos sounds like the efficient, savings-focused solution you've been seeking for your fulfilment needs, don't hesitate to reach out. Transform your business and unlock substantial savings with Bezos – your go-to fulfilment partner in the UK.
Get in touch now and have a chat with one of our savings specialists to tap into your company’s vast potential.
FAQ
What includes fulfilment?
Order fulfilment encompasses the entire process undertaken by a company from the moment a new order is received to the point of successfully delivering the product into the customer's possession. This comprehensive practice involves various stages such as warehousing, meticulously selecting and packing the product, and shipping.
How do you calculate the fulfilment cost per order?
Just divide your total order expenses by the total number of orders you received, and you’ll obtain your fulfilment cost per order (CPO).
How do you solve order fulfilment issues?
When it comes to solving order fulfilment issues, partnering up with an expert fulfilment company can be an effective solution. These companies are equipped with the knowledge, resources, and experience to address a wide range of challenges that may arise in the order fulfilment process.
Is fulfilment a fixed cost?
Not at all – all fulfilment costs are variable. In fact, most of them (such as fuel, labour, or rent) are likely to change over the years. That’s why you should always retain a certain degree of flexibility in your fulfilment budget.
Is fulfilment included in the cost of goods sold?
Yes, it is, although some companies make their customers pay for shipping separately. In a nutshell, the price of the goods you sell should reflect the cost of the fulfilment process.