Logistics KPIs and Metrics: A Complete Guide for Operational Success
In logistics, success isn’t just about moving goods from A to B — it’s about doing it smarter, faster, and more efficiently than the competition. But how do you measure success? The answer lies in tracking the right logistics KPIs (key performance indicators). These KPIs are the lifeblood of any logistics operation, revealing the areas where you’re excelling and the areas where there’s room for improvement.
In this article, we’ll explore key logistics KPIs across all stages of logistics with optimisation tips included. We’ll also show you how to set effective KPIs for logistics and track them. And finally, we’ll introduce you to Bezos, a Fulfilment-as-a-Service (FaaS) platform designed to streamline your logistics and give your business the edge it needs to stay ahead in a competitive market.
What Is a Logistics KPI?
Logistics KPIs are measurable values that help businesses assess the effectiveness and efficiency of their logistics operations. These indicators can provide insights into every logistics stage, such as order, supply, and transportation management, enabling companies to monitor performance and make data-driven decisions across the entire logistics process.
Are Logistics Metrics and KPIs the Same?
While the terms “metrics” and “KPIs” are often used interchangeably, there is a key difference between them. All KPIs are metrics, but not all metrics qualify as KPIs. Logistics metrics can refer to any data point that tracks logistics activities, such as the number of shipments or fuel consumption. However, logistics KPIs are more focused and strategic — they are the specific indicators that align directly with business goals, offering a clear picture of how well logistics operations are supporting overall objectives.
For example, while a metric might track total orders shipped, a KPI would measure the percentage of orders delivered on time. This distinction makes KPIs essential for identifying areas of improvement and driving operational success.
Why Are Logistics KPIs Important?
Measuring logistics KPIs is essential for driving operational improvements and achieving strategic goals. Here’s how tracking KPIs can benefit your business:
- Boost Efficiency: By pinpointing areas where processes slow down, such as delays in order handling or transport, KPIs help streamline operations, leading to faster, smoother logistics.
- Cut Costs: Monitoring KPIs related to transportation, warehousing, and inventory reveals cost-saving opportunities, allowing businesses to reduce unnecessary expenses without sacrificing quality.
- Improve Customer Satisfaction: Delivering orders on time and accurately is critical to customer loyalty. Tracking KPIs like On-Time Delivery Rate and Order Accuracy Rate ensures that you consistently meet or exceed customer expectations.
- Make Smarter Decisions: KPI data provides clear insights, enabling businesses to respond quickly to challenges and make informed decisions that drive performance improvements.
- Stay Aligned With Business Goals: KPIs give you a measurable way to track progress toward specific logistics goals, ensuring your efforts are aligned with overall business objectives.
The 5 Stages of Logistics to Measure With KPIs
Tracking logistics KPIs across all stages of the logistics process ensures businesses can optimise performance from start to finish. Below is an overview of the five crucial stages that should be measured:
Top 21 KPIs for Logistics
By tracking the most impactful logistics KPIs at each stage, you gain actionable insights that drive continuous improvement across your operations. Below, we outline 21 of the best KPIs to measure, divided into the five key stages in the logistics process. We outline what each logistics KPI means, the formula to calculate them, and how you can optimise them.
Order Management KPIs for Logistics (Administrative Process)
1. Order Processing Time
- Definition: This logistics KPI tracks how long it takes to process an order from the moment it is received until all administrative tasks, such as verifying details and confirming payment, are completed. It helps assess the efficiency of your order management process.
- Formula:
Order Processing Time = (Sum of Processing Times for All Orders) / (Total Number of Orders)
- Example: If the processing times for 5 orders are 2 hours, 3 hours, 2.5 hours, 4 hours, and 3 hours, the average Order Processing Time would be: (2 + 3 + 2.5 + 4 + 3) / 5 = 2.9 hours
- How to Improve: There are several ways you could optimise this KPI. For instance, tactics involve implementing automation tools for order processing, streamlining manual verification steps, and training staff on faster order-handling techniques to reduce bottlenecks.
2. Order Cancellation Rate
- Definition: The percentage of orders that are cancelled after submission but before the transaction is complete. This helps identify potential issues that lead to cancellations, such as product availability or customer satisfaction concerns.
- Formula:
Order Cancellation Rate = (Number of Cancelled Orders / Total Number of Orders Received) × 100
- Example: If you received 1,000 orders and 50 were cancelled, the Order Cancellation Rate would be: (50 / 1,000) × 100 = 5%
- How to Improve: Reducing cancellation rates involves ensuring product availability, providing clear information on stock and shipping times, and improving communication with customers about their orders.
Check out our other article for insights into advanced shipping logistics!
Supply Management Logistic KPIs (Supplier Performance & Procurement)
3. Supplier On-Time Delivery Rate
- Definition: The percentage of supplier deliveries that arrive on or before the agreed delivery date. This logistics KPI is crucial for ensuring a smooth supply chain and preventing delays in production or fulfilment.
- Formula:
Supplier On-Time Delivery Rate = (Number of On-Time Deliveries / Total Number of Deliveries) × 100
- Example: If you received 500 deliveries from suppliers and 450 of them were on time, the Supplier On-Time Delivery Rate would be: (450 / 500) × 100 = 90%
- How to Improve: To improve this KPI, consider collaborating closely with suppliers to set realistic delivery schedules, monitor performance regularly, and establish penalties or incentives for meeting deadlines.
4. Supplier Lead Time
- Definition: The amount of time that elapses between the moment a supplier receives an order and when the order is shipped. This KPI helps assess supplier efficiency and is crucial for ensuring timely deliveries.
- Formula:
Supplier Lead Time = (Sum of Lead Times for All Orders) / (Total Number of Orders)
- Example: If three suppliers took 10, 12, and 14 days from receiving the order to shipping, the average Supplier Lead Time would be: (10 + 12 + 14) / 3 = 12 days
- How to Improve: Reducing this logistics KPI can be achieved by negotiating faster fulfilment terms with suppliers, maintaining consistent communication, and collaborating with suppliers to identify inefficiencies.
5. Supplier Defect Rate
- Definition: The percentage of defective goods received from suppliers. This KPI helps identify issues with supplier quality and allows businesses to address recurring problems.
- Formula:
Supplier Defect Rate = (Number of Defective Units / Total Units Received) × 100
- Example: If you received 10,000 units and 200 of them were defective, the Supplier Defect Rate would be: (200 / 10,000) × 100 = 2%
- How to Improve: Regular supplier audits, setting clear quality standards, and fostering strong relationships with suppliers can help reduce the rate of defective goods received.
6. Supplier Compliance Rate
- Definition: This measures how often suppliers meet the agreed-upon contract terms, regulatory requirements, and industry standards. It ensures that suppliers are reliable and adhere to your business’s expectations.
- Formula:
Supplier Compliance Rate = (Number of Compliant Deliveries / Total Number of Deliveries) × 100
- Example: If a supplier met compliance requirements for 48 out of 50 deliveries in a given quarter, the Supplier Compliance Rate would be: (48 / 50) × 100 = 96%
- How to Improve: Improving supplier compliance involves setting clear expectations, conducting regular performance reviews, and maintaining open communication to address any issues that arise.
Inventory Control KPIs for Logistics (Stock Management)
7. Inventory Turnover Ratio
- Definition: Measures how many times a company sells and replaces its inventory within a given period. It’s a key indicator of inventory efficiency and demand for products.
- Formula:
Inventory Turnover Ratio = Cost of Goods Sold (COGS) / Average Inventory
- Example: If your COGS is £500,000 and your average inventory is £100,000, your Inventory Turnover Ratio would be: 500,000 / 100,000 = 5
- How to Improve: Improve this logistics KPI by managing stock levels more closely, reducing slow-moving inventory, and aligning inventory levels with demand forecasts.
8. Inventory Accuracy
- Definition: The percentage of inventory that matches the recorded stock levels in your system. It reflects how accurately a company tracks and manages its inventory.
- Formula:
Inventory Accuracy = (Counted Items / Items on Record) × 100
- Example: If you counted 950 items and your system recorded 1,000 items, the Inventory Accuracy would be: (950 / 1,000) × 100 = 95%
- How to Improve: Improve accuracy by performing regular cycle counts, using barcode scanning or RFID technology, and minimising manual entry errors during stock updates.
9. Days of Inventory on Hand (DOH)
- Definition: This KPI for logistics measures the average number of days inventory is held before it’s sold or used. It indicates how efficiently a company is managing its stock levels.
- Formula:
DOH = (Average Inventory / Cost of Goods Sold) × 365
- Example: If your average inventory is £120,000 and your COGS is £600,000, the DOH would be: (120,000 / 600,000) × 365 = 73 days
- How to Improve: Reduce DOH by improving demand forecasting, optimising reorder points, and reducing excess inventory through better purchasing strategies.
10. Backorder Rate
- Definition: The percentage of orders that cannot be fulfilled due to insufficient stock. It highlights inventory shortages and their impact on customer satisfaction.
- Formula:
Backorder Rate = (Number of Backorders / Total Number of Orders) × 100
- Example: If you received 1,000 orders and 100 of them could not be fulfilled due to stockouts, the Backorder Rate would be: (100 / 1,000) × 100 = 10%
- How to Improve: To reduce the Backorder Rate, improve inventory planning, enhance demand forecasting, and maintain safety stock levels to avoid stockouts.
11. Inventory Carrying Cost
- Definition: This logistics KPI measures the total cost of holding inventory, including storage, insurance, depreciation, and opportunity costs. It helps businesses understand the financial impact of maintaining inventory.
- Formula:
Inventory Carrying Cost = (Inventory Holding Costs / Total Value of Inventory) × 100
- Example: If your inventory holding costs are £40,000 and the total value of your inventory is £400,000, the Inventory Carrying Cost would be: (40,000 / 400,000) × 100 = 10%
- How to Improve: Reduce carrying costs by lowering excess inventory, improving stock turnover, and negotiating better storage and insurance rates.
Distribution Operations KPIs for Logistics (Physical Fulfilment)
12. Order Accuracy Rate
- Definition: The percentage of customer orders that are picked, packed, and shipped without errors. It’s a key indicator of the effectiveness of distribution operations, ensuring that the correct items are sent in the right quantities.
- Formula:
Order Accuracy Rate = (Number of Error-Free Orders / Total Number of Orders) × 100
- Example: If you processed 2,000 orders and 1,900 were error-free, the Order Accuracy Rate would be: (1,900 / 2,000) × 100 = 95%
- How to Improve: Improving this KPI for logistics involves better training for staff on picking and packing procedures, implementing barcode scanning for accuracy, and refining quality control measures before shipment.
13. Pick and Pack Cycle Time
- Definition: This KPI measures the amount of time it takes to pick items from inventory and pack them for shipment. A shorter cycle time indicates a more efficient fulfilment process.
- Formula:
Pick and Pack Cycle Time = Time Packing is Completed - Time Order Was Picked in Warehouse
- Example: If an order was picked at 10:00 AM and packed by 11:30 AM, the Pick and Pack Cycle Time would be: 11:30 AM - 10:00 AM = 1.5 hours
- How to Improve: Improve this logistics KPI by optimising warehouse layout, introducing automation, and refining picking and packing workflows.
14. Order Fill Rate
- Definition: Order Fill Rate measures the percentage of customer orders that are fulfilled completely without any backorders or stockouts. A higher fill rate indicates better stock management and customer satisfaction.
- Formula:
Order Fill Rate = (Number of Orders Fulfilled Completely / Total Number of Orders) × 100
- Example: If 850 out of 1,000 orders were fulfilled without stockouts, the Order Fill Rate would be: (850 / 1,000) × 100 = 85%
- How to Improve: To improve this logistics KPI, focus on better demand forecasting, managing inventory levels effectively, and reducing stockouts.
15. Perfect Order Rate
- Definition: This KPI measures the percentage of orders that are delivered on time, complete, undamaged, and with accurate documentation. It’s a critical indicator of overall operational excellence in distribution.
- Formula:
Perfect Order Rate = (Number of Perfect Orders / Total Number of Orders) × 100
- Example: If you delivered 950 perfect orders out of 1,000 total orders, the Perfect Order Rate would be: (950 / 1,000) × 100 = 95%
- How to Improve: To boost the Perfect Order Rate, focus on improving accuracy at every stage of the fulfilment process, maintain quality checks, and ensure delivery partners meet high standards for on-time and damage-free shipping.
16. Warehouse Space Utilisation
- Definition: This logistics KPI measures the percentage of warehouse space effectively used for storage and operations. This helps monitor how efficiently space is utilised in the warehouse.
- Formula:
Warehouse Space Utilisation = (Space Used for Storage / Total Warehouse Space) × 100
- Example: If you use 60,000 out of 80,000 square feet of space, your Warehouse Space Utilisation would be: (60,000 / 80,000) × 100 = 75%
- How to Improve: To improve this KPI, optimise warehouse layout, reduce excess stock, and make better use of vertical space with improved racking systems.
Transport Management Logistics KPIs (Delivery and Transport Efficiency)
17. On-Time Delivery Rate
- Definition: The percentage of deliveries made to customers on or before the promised delivery date. This logistics KPI is critical for measuring the efficiency and reliability of the transportation process.
- Formula:
On-Time Delivery Rate = (Number of On-Time Deliveries / Total Number of Deliveries) × 100
- Example: If 900 out of 1,000 deliveries were made on time, the On-Time Delivery Rate would be: (900 / 1,000) × 100 = 90%
- How to Improve: To improve this, work closely with carriers to optimise delivery schedules, monitor traffic and route conditions, and communicate with customers to manage expectations.
18. Freight Cost per Unit
- Definition: The average cost of transporting goods per unit, helping businesses manage transportation expenses effectively.
- Formula:
Freight Cost per Unit = Total Freight Costs / Total Units Shipped
- Example: If your total freight costs were £50,000 and you shipped 10,000 units, the Freight Cost per Unit would be: 50,000 / 10,000 = £5 per unit
- How to Improve: Improve this logistics KPI by consolidating shipments, negotiating better rates with carriers, and optimising load capacity to reduce overall costs.
19. Truck Turnaround Time
- Definition: The time taken for trucks to load, unload, and leave a warehouse or distribution centre. This logistics KPI measures the efficiency of loading and unloading operations.
- Formula:
Truck Turnaround Time = Time Truck Departs - Time Truck Arrives at Warehouse
- Example: If a truck arrives at 8:00 AM and leaves by 9:00 AM, the Truck Turnaround Time would be: 9:00 AM - 8:00 AM = 1 hour
- How to Improve: Reduce Truck Turnaround Time by streamlining loading and unloading procedures, ensuring adequate staffing, and improving warehouse layout to allow smoother truck movements.
20. Fuel Efficiency
- Definition: This measures fuel consumption during transportation, commonly expressed as miles per gallon. It helps track how efficiently transportation resources are being used.
- Formula:
Fuel Efficiency = Miles Driven / Gallons of Fuel Consumed
- Example: If a truck drove 600 miles using 50 gallons of fuel, the Fuel Efficiency would be: 600 / 50 = 12 miles per gallon
- How to Improve: To improve Fuel Efficiency, optimise delivery routes, use fuel-efficient vehicles, and ensure drivers follow best practices for fuel conservation.
21. Average Days Late
- Definition: The average number of days that deliveries are late, providing insight into delays in the logistics and transport process.
- Formula:
Average Days Late = (Sum of Days Late for All Deliveries / Total Number of Late Deliveries)
- Example: If 5 deliveries were late by a total of 15 days, the Average Days Late would be: 15 / 5 = 3 days late on average
- How to Improve: Improve this logistics KPI by working with carriers to reduce delays, monitoring traffic patterns, and proactively adjusting delivery schedules based on anticipated disruptions.
How to Set Effective KPIs for Logistics: Top Tips
Now that we have finished our list of 21 top logistics KPIs, let’s consider how to decide which ones to set up and track. Here are a few top tips on how to set KPIs that truly make a difference:
- Set SMART Goals Aligned With Business Objectives: Define clear, specific logistics goals that support your company’s broader objectives, and ensure they follow the SMART framework (Specific, Measurable, Achievable, Relevant, and Time-Bound). For example, instead of simply aiming to “improve delivery efficiency,” set a goal like “increase On-Time Delivery Rate to 95% within three months” to ensure the KPI is both measurable and tied to a concrete business outcome.
- Leverage Industry Benchmarks: In addition to evaluating your internal performance, compare your logistics operations with industry benchmarks. By analysing how successful companies — even those outside your sector — perform in key areas, you can identify strengths and weaknesses in your own strategies. This insight helps you set more informed, achievable goals and stay ahead of industry trends.
- Prioritise Key KPIs: Avoid the temptation to track too many KPIs at once. Instead, focus on the most important ones for each stage of your logistics operations, such as Order Cancellation Rate for order management or Freight Cost per Unit for transport management.
- Regularly Review and Analyse KPIs: Setting effective KPIs is just the beginning — continuous monitoring and analysis are key to long-term success. Regularly reviewing your logistics KPIs allows you to track progress, identify emerging issues, and make informed adjustments that drive ongoing operational improvements.
How to Track and Measure Logistics KPIs
Tracking and measuring logistics KPIs requires tools. Two of the most powerful are scorecards and dashboards, which each serve different but complementary purposes:
- Scorecards for Tracking KPIs: Scorecards offer a snapshot of how well your logistics operations are meeting set targets. They allow you to see how your performance measures up against predefined goals. Unlike dashboards, scorecards focus more on progress toward longer-term objectives rather than real-time data.
- Dashboards for Real-Time Monitoring: Dashboards, on the other hand, focus on real-time data, providing immediate insights into operations. They present KPIs visually through graphs, charts, and tables, making it easy to quickly spot trends, bottlenecks, or issues as they happen. Dashboards can be customised to suit different logistics stages, allowing users to drill down into specifics and make faster decisions. A well-designed dashboard helps logistics teams stay on top of day-to-day operations and respond proactively to any emerging issues.
The key difference between scorecards and dashboards is that scorecards are better for managing your strategy, whereas dashboards are better for managing your operations.
Best Practices for Using Scorecards and Dashboards
Here are some practical tips for setting up effective dashboards and scorecards for logistics KPIs:
- Customise for Your Audience: Tailor dashboards and scorecards to different roles within your organisation. For example, warehouse managers may need to focus on space utilisation, while transport managers should see delivery and fuel efficiency.
- Use Clear Visuals: Ensure charts, graphs, and visuals are easy to interpret. Avoid clutter and focus on clear, impactful presentations of data.
- Automate Data Updates: Use systems that automatically pull in real-time data to keep dashboards current, reducing manual input and ensuring accuracy.
- Focus on Actionable Insights: Design dashboards and scorecards to not only present information but also to highlight key areas where immediate action is needed.
- Review and Adjust Regularly: Regularly review your dashboards and scorecards to ensure they’re still aligned with your logistics objectives and provide the insights you need.
Run Your Logistics Effortlessly With Bezos
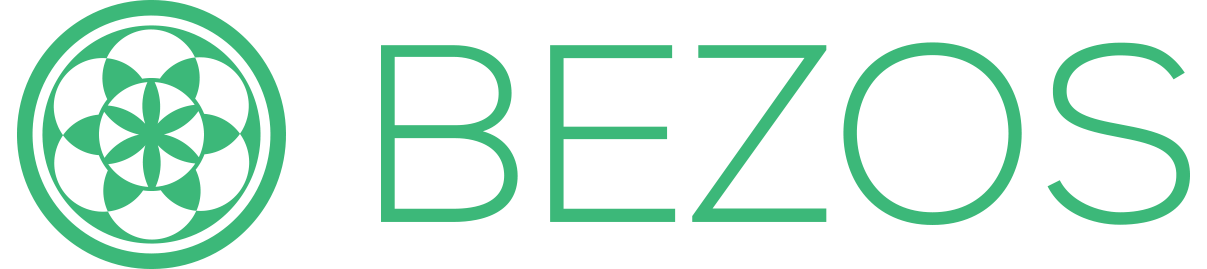
At Bezos, we specialise in providing streamlined fulfilment services that empower eCommerce businesses to optimise their logistics operations, helping you meet your business goals more efficiently. Our technology-driven approach enhances every aspect of your fulfilment process, ensuring that your logistics run smoothly so you can focus on growth.
Here’s how partnering with Bezos enhances your logistics operations:
- End-to-End Fulfilment: We manage everything from receiving and storing inventory to picking, packing, and shipping orders. This full-service approach reduces delays, minimises errors, and keeps your logistics running smoothly from start to finish. By outsourcing your logistics to us, you save time, reduce operational complexity, and boost overall efficiency.
- Dedicated Support: All of our customers get a dedicated account manager to assist with managing their orders, so you always have expert, 24/7 support on hand.
- Seamless Multi-Channel Integration: Bezos integrates with over 30 platforms, including Shopify, eBay, and Amazon. This means you can manage orders across all your sales channels from one platform, simplifying your processes and maintaining a consistent flow of goods to your customers.
- Track Order Statuses: Our software lets you access all inventory and order information in real-time so that you can monitor the status of every order.
- Global Reach With Local Expertise: Whether shipping domestically or internationally, our global network of fulfilment centres ensures fast and reliable deliveries. Plus, our late cut-off times for same-day dispatch allow you to maintain speed and customer satisfaction, no matter where your customers are located.
- Bespoke Fulfilment Solutions: We understand that every business is different. That’s why Bezos offers tailored solutions to meet your specific logistics needs. From custom packaging to flexible returns solutions, we align our services with your business goals to enhance efficiency and boost customer satisfaction.
By choosing Bezos, you gain a partner dedicated to optimising your eCommerce logistics operations, helping you scale your business, reduce costs, and deliver an exceptional customer experience.
Conclusion: Mastering Logistics KPIs for Optimal Performance
Achieving optimal logistics performance starts with tracking the right logistics KPIs. By consistently monitoring and refining these key indicators, you can optimise processes, enhance overall efficiency, and improve customer experiences. For eCommerce brands looking to simplify this, Bezos provides the technology and expertise to streamline your logistics operations. Partner with Bezos and turn your logistics KPIs into a competitive advantage — because when your logistics run like clockwork, your business has room to grow.
FAQ
What is a KPI in logistics?
A KPI in logistics is a measurable indicator used to evaluate the performance and efficiency of logistics processes, like Order Cancellation Rate or Inventory Accuracy.
What are the 7 C’s of logistics?
The 7 C’s — Connect, Create, Customise, Coordinate, Consolidate, Collaborate, and Contribute — is a framework that represents a comprehensive approach to managing logistics and ensuring an efficient, integrated supply chain.